The design and material of the tubing or hose in a peristaltic pump head have a significant impact on the pump’s performance and its compatibility with different fluids. Here’s how the tubing design and material influence these factors:
- Flexibility and Resilience: The flexibility of the tubing affects the pump’s ability to squeeze and release fluid. More flexible tubing can create a stronger peristaltic action, providing better fluid displacement. Resilient tubing rebounds after compression, preventing backflow and improving dosing accuracy.
- Tubing Diameter: The inner diameter of the tubing determines the flow rate of the pump. Larger diameters allow for higher flow rates, while smaller diameters reduce flow. The choice of diameter depends on the desired flow rate for the specific application.
- Wall Thickness: The thickness of the tubing wall affects its durability and resistance to wear and tear. Thicker walls are more durable but may reduce the pump’s flexibility. Thinner walls offer greater flexibility but may be less robust.
- Material Compatibility: The choice of tubing material is critical for compatibility with the fluid being pumped. Different materials offer resistance to specific chemicals, solvents, and abrasion. Common materials include silicone, Tygon®, PharMed®, and various other elastomers or plastics.
- Chemical Resistance: Tubing materials should be carefully selected to resist the corrosive or reactive properties of the fluid being pumped. Some materials are compatible with a wide range of chemicals, while others are tailored for specific applications.
- Biocompatibility: In medical and bioprocessing applications, tubing materials must be biocompatible to prevent contamination of the fluid and ensure safety when handling biological or pharmaceutical substances.
- Temperature Resistance: Tubing materials must withstand the temperature conditions of the application. High-temperature materials are needed for hot fluids, while low-temperature materials are required for cold environments.
- Abrasion Resistance: In applications where the fluid contains abrasive particles or is subject to mechanical wear, tubing materials should be abrasion-resistant to prolong tubing life.
- Transparency and Clarity: In some applications, it’s important for users to visually inspect the fluid in the tubing. Transparent or clear tubing materials allow for easy visual monitoring.
- Compliance and Certifications: Depending on the industry and application, tubing materials may need to meet specific compliance and certification standards, such as FDA approval for food and pharmaceutical applications.
- Maintenance and Replacement: The ease of tubing replacement can affect the overall maintenance of the peristaltic pump. Quick-change tubing systems simplify tubing replacement, minimizing downtime.
- Sterilizability: In applications requiring aseptic conditions, tubing materials should be sterilizable to prevent contamination. Some materials are autoclavable, gamma-sterilizable, or compatible with chemical sterilization.
The choice of tubing material and design should be based on the specific requirements of the application, taking into consideration factors such as the fluid properties, flow rate, temperature, chemical compatibility, and any regulatory or safety considerations. The right tubing selection is crucial for optimizing pump performance and ensuring the longevity of the tubing.
What advantages does a peristaltic pump head offer in terms of precise fluid dosing and minimizing contamination risks?
Peristaltic pump heads offer several advantages when it comes to precise fluid dosing and minimizing contamination risks, making them ideal for a wide range of applications, including pharmaceuticals, biotechnology, chemical processing, and food production. Here are the key advantages:
Dosing Accuracy: Peristaltic pump heads provide highly accurate dosing and dispensing of fluids. The squeezing action of the tubing creates a consistent and repeatable flow, making them suitable for applications where precise volumes are critical.
Minimal Contamination Risk: Peristaltic pumps are designed to prevent the fluid from coming into contact with pump components, minimizing the risk of contamination. China Peristaltic Pump Head suppliers Fluid only touches the inside of the tubing, ensuring the integrity and purity of the sample.
Ease of Cleaning: Peristaltic pump heads are relatively easy to clean and sterilize, especially in applications that require aseptic conditions. Users can replace the tubing and sanitize the pump head quickly, reducing the risk of cross-contamination between different samples.
Wide Range of Tubing Materials: Peristaltic pumps can be fitted with various tubing materials to suit the needs of different applications. Users can select tubing that is compatible with specific chemicals, solvents, or biological fluids, minimizing the risk of material interactions or corrosion.
No Valves or Seals: Unlike some other types of pumps, peristaltic pump heads do not require valves or seals that can wear out or leak, reducing the risk of fluid leakage and contamination.
Versatility: Peristaltic pumps can handle a broad range of viscosities, from very low to highly viscous fluids, without the need for major adjustments. This versatility makes them suitable for a wide variety of applications.
Continuous Flow: The peristaltic action of these pumps ensures a smooth and continuous flow of fluid without pulsations or flow interruptions, improving the precision of dosing.
Easy Tubing Replacement: Changing the tubing is a straightforward process in peristaltic pumps, reducing downtime during maintenance. Quick-change tubing systems simplify tubing replacement.
Remote and Programmable Control: Peristaltic pumps often have remote and programmable control options, allowing users to set precise dosing parameters and monitor the pump’s performance from a distance.
Elimination of Dead Volume: Peristaltic pump heads have minimal dead volume, meaning that nearly all of the fluid in the tubing is dispensed, reducing waste and ensuring accurate dosing.
Reduced Exposure to Hazardous Materials: In applications involving hazardous or toxic materials, peristaltic pump heads minimize operator exposure to these substances, enhancing safety.
Long Tubing Life: Peristaltic tubing typically has a longer service life compared to some other pump components, reducing the frequency of replacements and maintenance.
Sample Integrity: Peristaltic pump heads are suitable for applications where sample integrity is crucial, such as in analytical chemistry or pharmaceutical manufacturing.
These advantages make peristaltic pump heads a preferred choice for applications that demand precise fluid dosing and a high level of contamination control. Their accuracy, versatility, and ease of maintenance contribute to efficient and reliable fluid handling while minimizing the risk of cross-contamination.
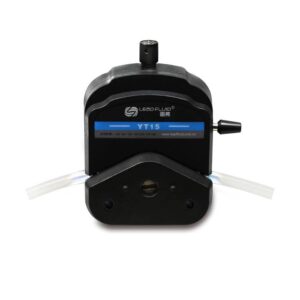