A sanitary napkin machine is a type of manufacturing equipment that is used to produce sanitary napkins, which are disposable products used for feminine hygiene. The machine is typically used by companies that produce menstrual hygiene products and can vary in size and complexity depending on the desired output and level of automation.
Here are some of the basic components and features of a typical sanitary napkin machine:
Raw material feeding system: This system is used to feed raw materials into the machine, including the absorbent core material, top sheet material, and bottom sheet material.
Converting system: This system converts the raw materials into finished sanitary napkins, using a combination of cutting, sanitary napkin machine folding, and sealing processes.
Control panel: The control panel allows operators to monitor and adjust various settings on the machine, such as the speed of production and the length of the napkin.
Conveyor system: The conveyor system moves the finished sanitary napkins from the machine to a packaging or storage area.
Optional features: Some sanitary napkin machines may include additional features, such as automatic splicing of raw materials, automatic quality control systems, and automatic rejection systems for defective products.
Sanitary napkin machines can vary in price and complexity depending on the desired output and level of automation. Some machines may be designed for small-scale production, while others are designed for large-scale commercial production. It’s important to choose a machine that is appropriate for your production needs and budget, and to ensure that it meets all relevant safety and quality standards.
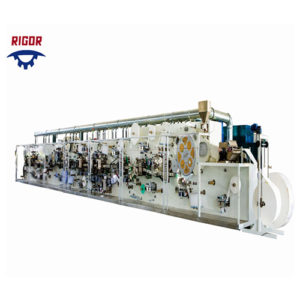
Manufacturers use several methods to ensure the quality of sanitary napkins during the production process.
Here are some common quality control measures:
Raw material quality check: Manufacturers check the quality of the raw materials used in the production of sanitary napkins, such as the absorbent core material, top sheet material, and bottom sheet material. This can include testing for absorbency, strength, and consistency.
Machine calibration: The machine used to produce the sanitary napkins is calibrated to ensure that it is operating at the correct speed and producing the desired product dimensions.
Inspection of finished products: Finished sanitary napkins are inspected to ensure that they meet the desired quality standards. This can include visual inspection and testing for absorbency, leakage, and overall product performance.
Sampling and testing: Manufacturers may take samples of the finished products and test them for quality and performance. This can include laboratory testing to measure product properties such as absorbency, fluid distribution, and leakage.
Quality management systems: Manufacturers may implement quality management systems such as ISO 9001 to ensure that their production processes are consistent and meet the desired quality standards.
Regulatory compliance: Sanitary napkin manufacturers must comply with regulatory standards and requirements, such as those set forth by the FDA or other regulatory agencies. Compliance with these standards helps ensure that the products are safe and effective for their intended use.
Overall, manufacturers use a combination of quality control measures to ensure that sanitary napkins are produced to the desired quality standards and meet regulatory requirements. These measures help ensure that the products are safe, effective, and meet the needs of users.