Rexroth is a well-known manufacturer of hydraulic pumps, which are used in a wide range of applications, including manufacturing, construction, agriculture, and transportation. Rexroth hydraulic pumps are known for their reliability, efficiency, and durability.
Here are some key features and benefits of Rexroth hydraulic pumps:
Wide range of models: Rexroth offers a wide range of hydraulic pump models to meet the needs of various applications, including fixed displacement pumps, variable displacement pumps, and axial piston pumps.
High efficiency: Rexroth hydraulic pumps are designed for high efficiency, which can help reduce energy consumption and operating costs.
Robust construction: Rexroth hydraulic pumps are built with high-quality materials and components, which can help ensure their durability and reliability in demanding applications.
Customizable options: Rexroth hydraulic pumps can be customized to meet specific application requirements, such as flow rate, pressure, and mounting options.
Easy maintenance: Rexroth hydraulic pumps are designed for easy maintenance, with features such as accessible filters and easy-to-replace components.
Industry-leading warranty: Rexroth offers an industry-leading warranty on its hydraulic pumps, which can give operators peace of mind and help protect their investment.
Overall, Rexroth hydraulic pumps are a reliable and efficient choice for a wide range of hydraulic applications. rexroth hydraulic pump It’s important to consult the manufacturer’s recommendations and guidelines for the proper installation, operation, and maintenance of your Rexroth hydraulic pump to ensure its efficient and reliable operation.
The choice of a specific Rexroth hydraulic pump model for a construction application would depend on several factors, including the required flow rate, pressure, and other application-specific requirements.
Here are some Rexroth hydraulic pump models that are commonly used in construction applications:
A10VO series axial piston pump: The A10VO series is a variable displacement axial piston pump that is known for its high efficiency and reliability. It is commonly used in mobile construction equipment, such as excavators, loaders, and bulldozers.
A4VG series axial piston pump: The A4VG series is a variable displacement axial piston pump that is known for its high power density and efficiency. It is commonly used in heavy-duty construction equipment, such as cranes, pavers, and road rollers.
AA10VSO series axial piston pump: The AA10VSO series is a variable displacement axial piston pump that is known for its low noise and high efficiency. It is commonly used in construction machinery, such as concrete pumps and drilling rigs.
A2FO series fixed displacement axial piston pump: The A2FO series is a fixed displacement axial piston pump that is known for its compact design and high efficiency. It is commonly used in construction equipment, such as forklifts and aerial work platforms.
It’s important to consult the manufacturer’s recommendations and guidelines for the proper selection and installation of your Rexroth hydraulic pump for your specific construction application. A Rexroth service technician can also provide guidance on the best hydraulic pump model for your specific needs.
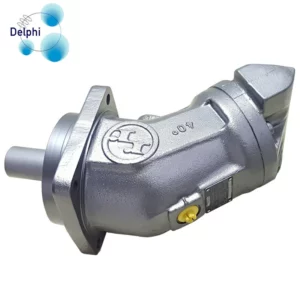